Spiders, surgery and sustainable silk
How spiders are helping innovation in surgery and environmental sustainability
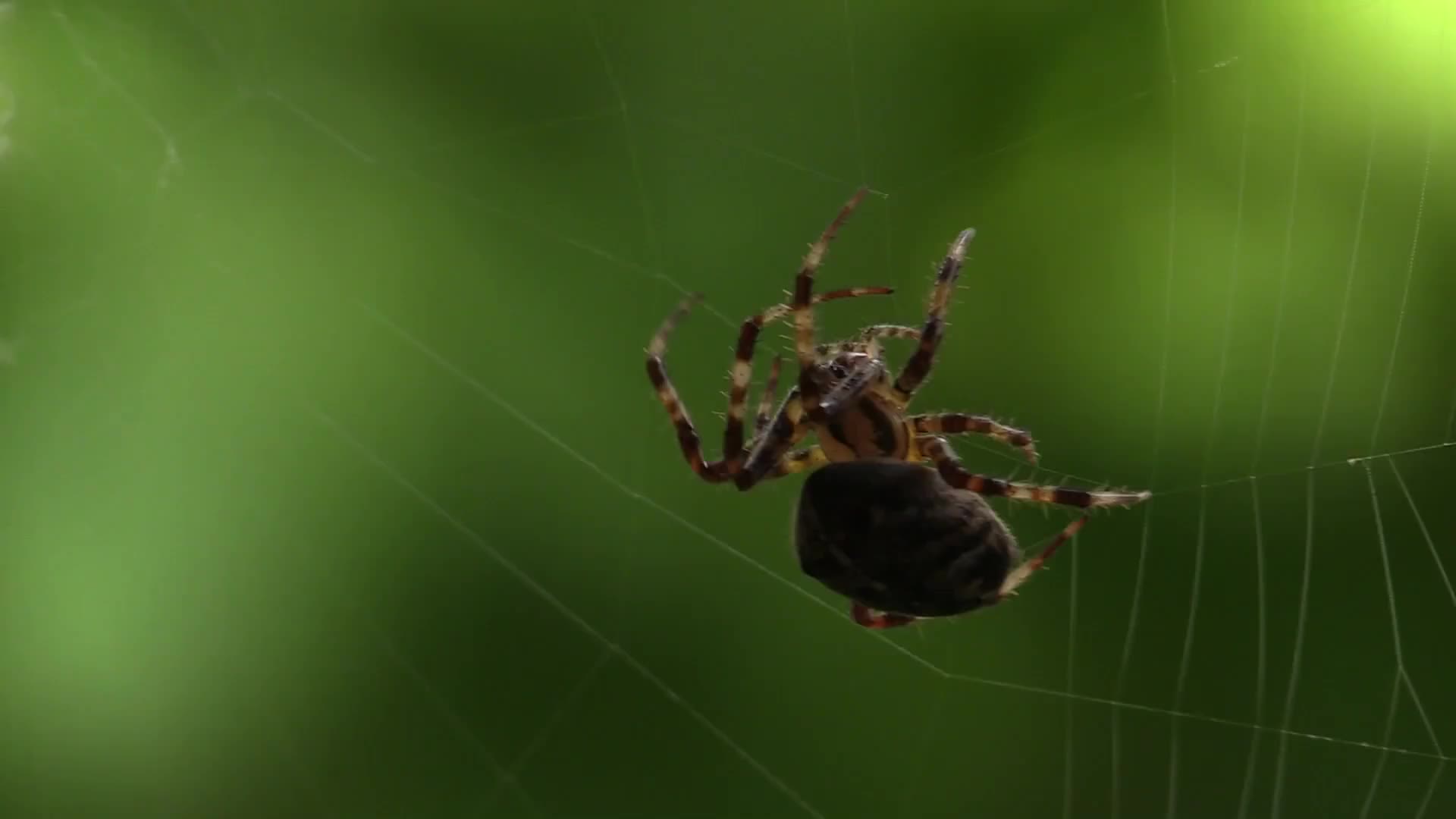
Research from the University of Oxford has led to innovations using and simulating spider silk, which are paving the way for surgeons to repair nerve damage and for the textile industry to reduce its environmental impact.
While there is much to be said for academics focussing research efforts into challenges posed by industry partners, primary research continues to play a vital role. This is not least in the field of bioinspiration and biomimetics where insights from biology are used to solve design challenges. Discoveries, such as how spiders produce silk, provide the basis for the investigation of a whole raft of potential commercial applications.
This approach of research first, applications later, led Fritz Vollrath, a Professor in Oxford’s Department of Biology, to understand that spiders spin different types of silk.
Professor Vollrath's investigations led to the formation of the Oxford Silk Group and of Oxford Biomaterials (OBM), a little over twenty years ago. The former being a research group and the latter a spinout company which now acts as a platform for new companies to find commercial applications in this field.
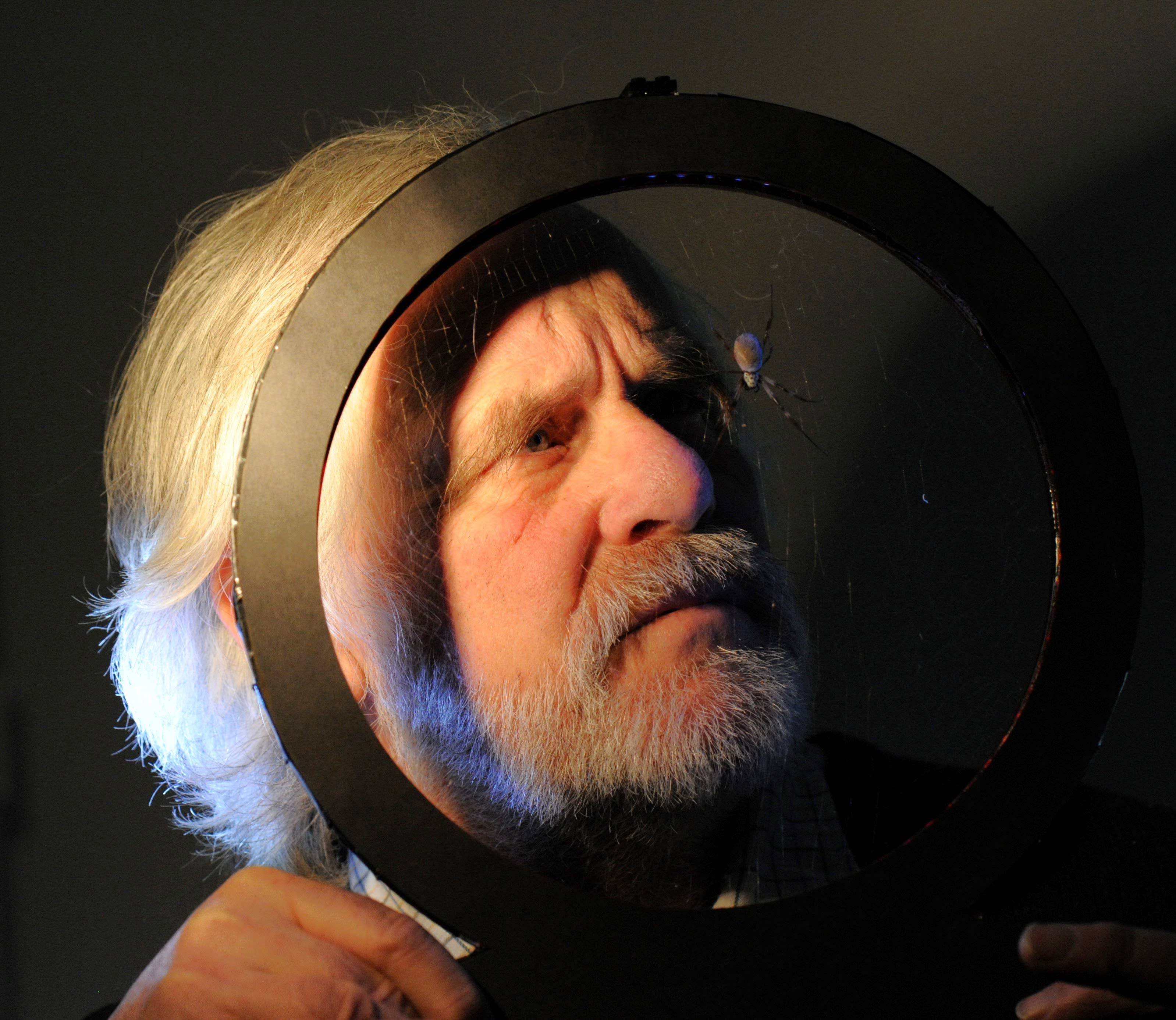
Silkworms, as well as spiders, are part of Professor Vollrath’s research because he is fascinated by how these two animals have independently developed the means to grow a material internally which is then ejected for multiple purposes.
To prove how promising silk can be for novel applications, Professor Vollrath has used silkworm silk to build a lightweight fighter pilot helmet for the US Air Force, as well as ‘ballistic knickers’ for the Ministry of Defence in the UK. The tough silk underwear not so much protects against the shrapnel impact of a landmine, but prevents dirt being blown into the body tissues and cavities, and thus protects against life threatening infections.
While these remain transformative concept projects, other primary research has led to the formation of dedicated spinout companies. For example Newrotex, a recent spinout from OBM, is developing a revolutionary new surgical device to provide a more effective way to repair nerve damage without the collateral damage of harvesting other nerves. It uses a silk tubing containing silk fibres which act as a ‘hand rail’ for two ends of a severed nerve to regrow across and reconnect.
Current pre-clinical trials are progressing well and could lead to human trials soon which, if successful, have the potential to see the pioneering approach being adopted before the end of 2025.
At Spintex, a spinout from the University of Oxford’s Department of Zoology (now Biology), rather than OBM, Professor Vollrath’s breakthrough is being applied to replicate the silk spinning process of a spider to create more environmentally-friendly silk. Having proved the concept, the business will soon start producing samples to demonstrate the possibilities when they scale-up operations.
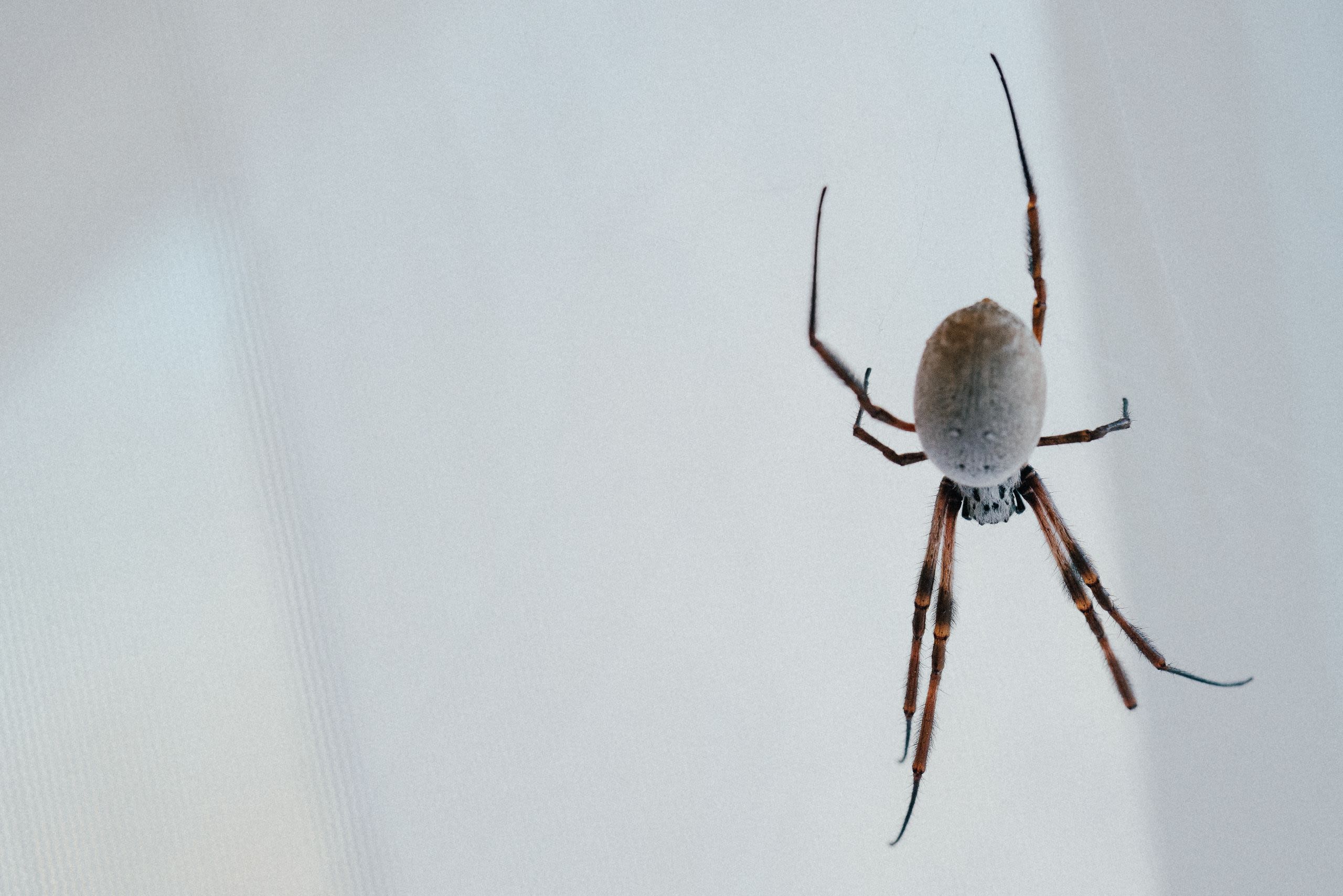
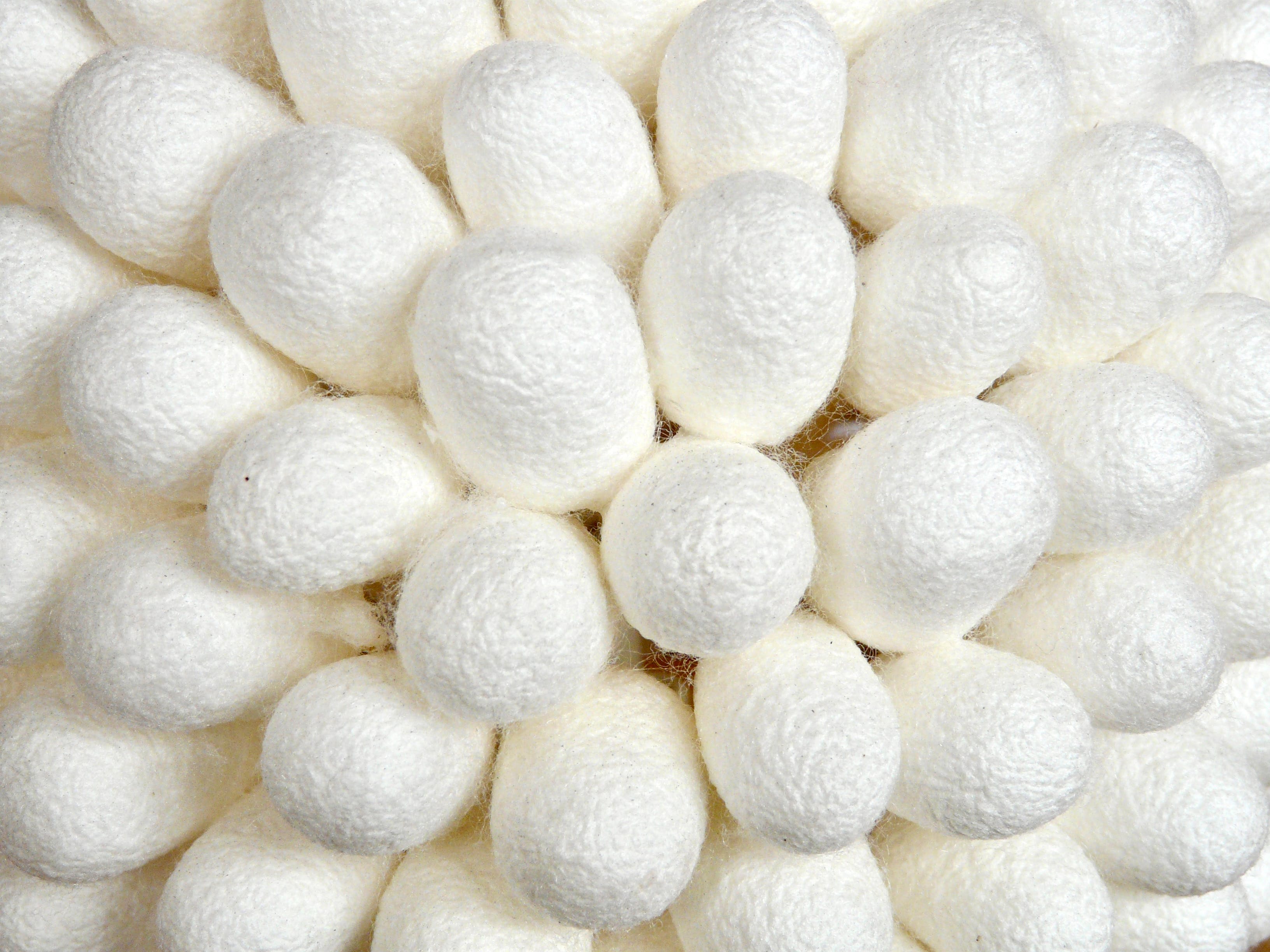
Unravelling the secrets of silk
The early research of Professor Vollrath was pioneering and considered significant enough to merit a prominent article in the eminent scientific journal Nature in 2001.
‘Spinning has been used by people for hundreds of years to make clothes. We understand the physics and chemistry of it but nobody had ever looked at this natural spinning system,’ he says.
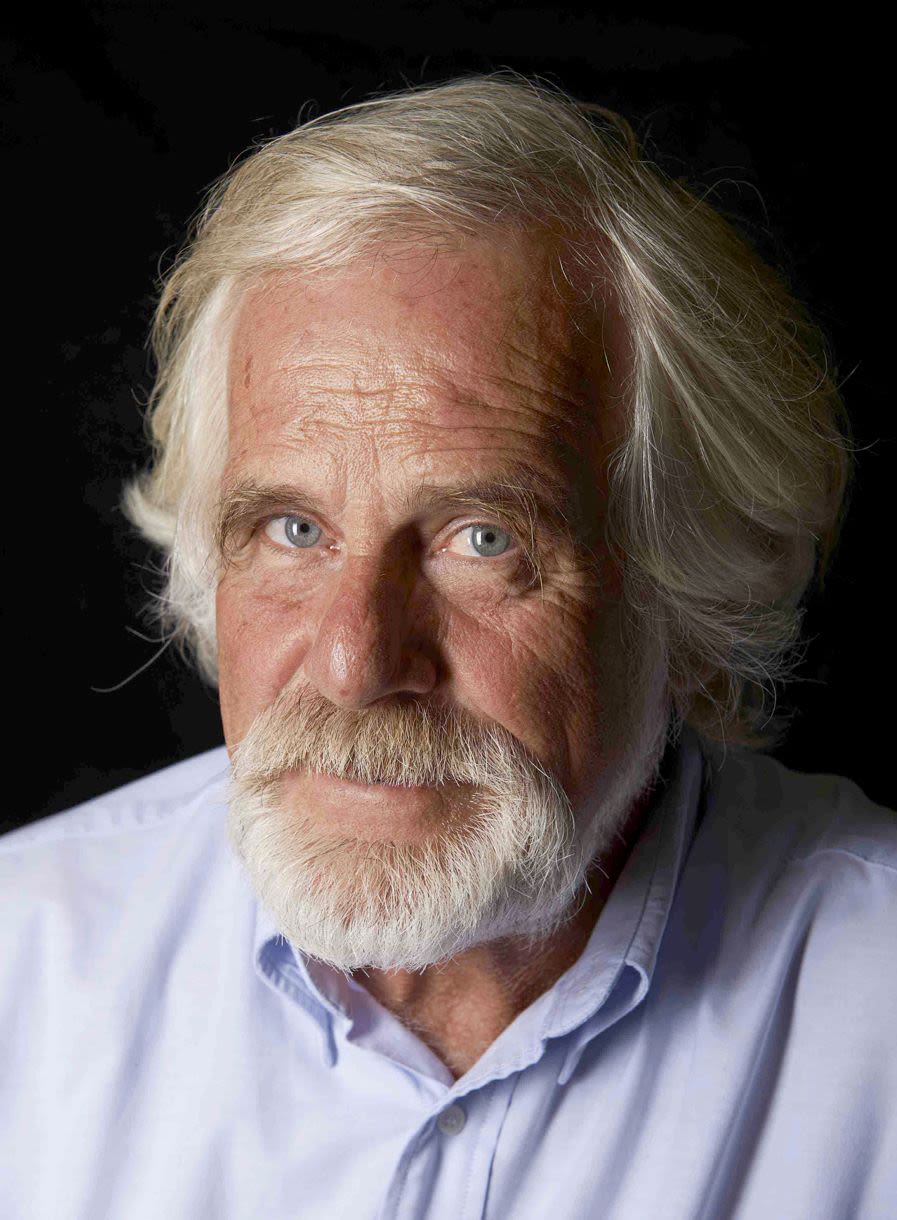
Professor Fritz Vollrath
Professor Fritz Vollrath
‘Spiders have found a way of making filaments that are tougher than Kevlar, in fact they’re better than any man-made material in nearly every way, and they’re made in a far more energy-efficient way than any petro-chemical process we have. They simply get the right molecules lined up and then stretch them.’
The discovery of how a spider uses molecules and excretes them to produce up to seven different types of silk, led to the University of Oxford licensing the breakthrough. It invested in Spinox Ltd a little over twenty years ago and was soon joined by a subsequent investment from a German financial company.
Spinox was later bought out by the investors interested in using the tech to spin silk on an industrial scale. This prompted the revival and re-financing of the follow-up Oxford spinout, Oxford Biomaterials Ltd, with a refocus of interest in bio-medical applications of silks.
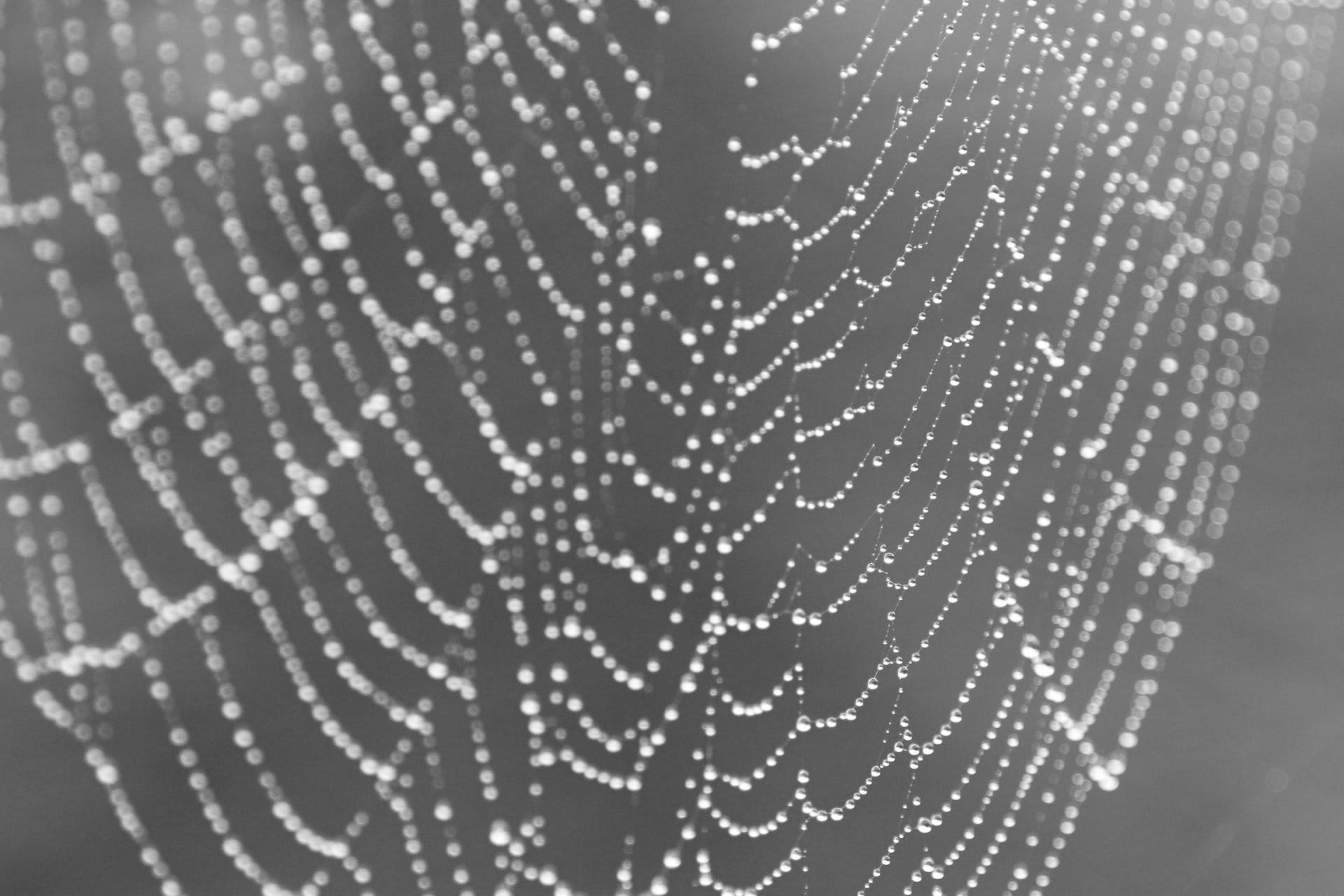
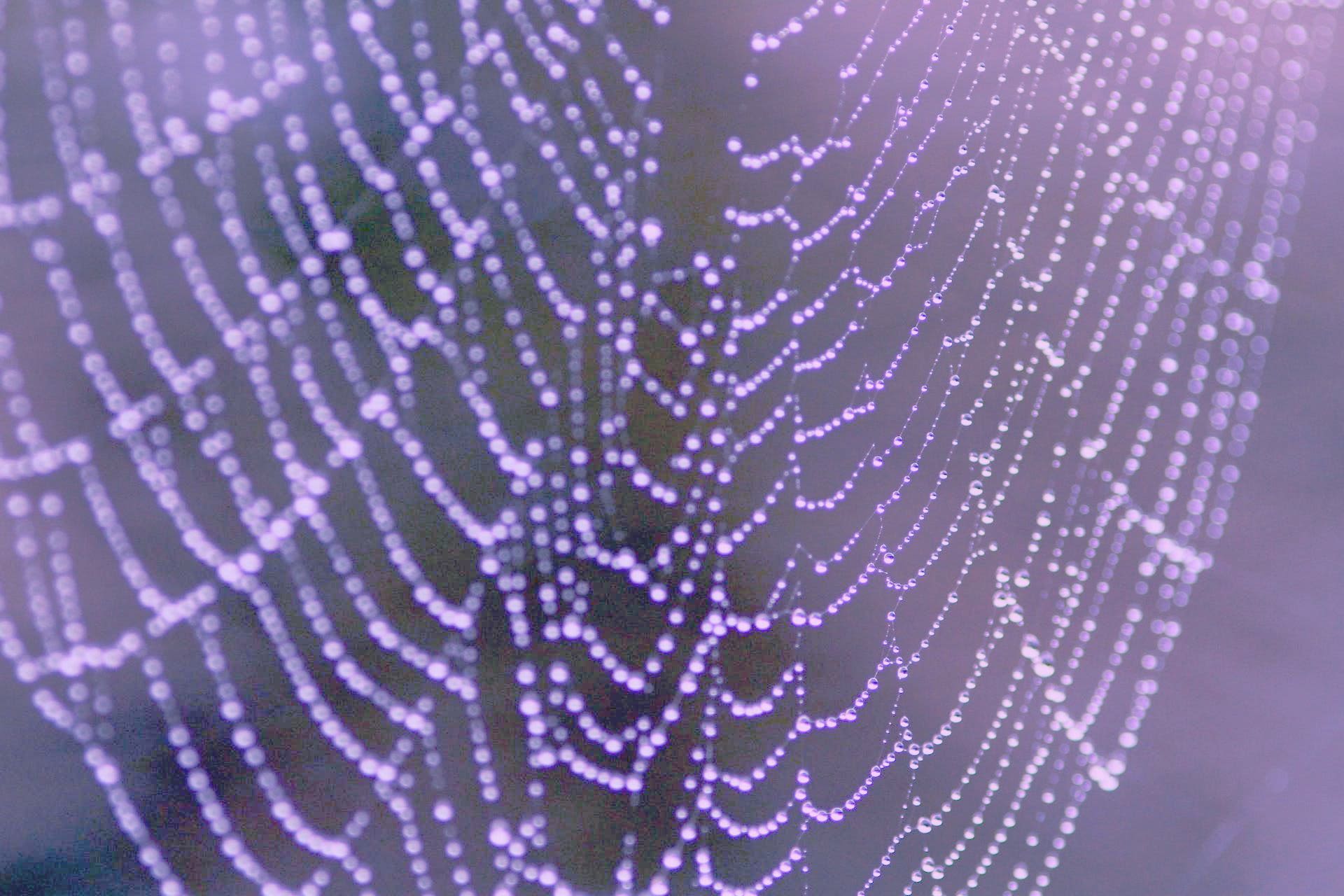
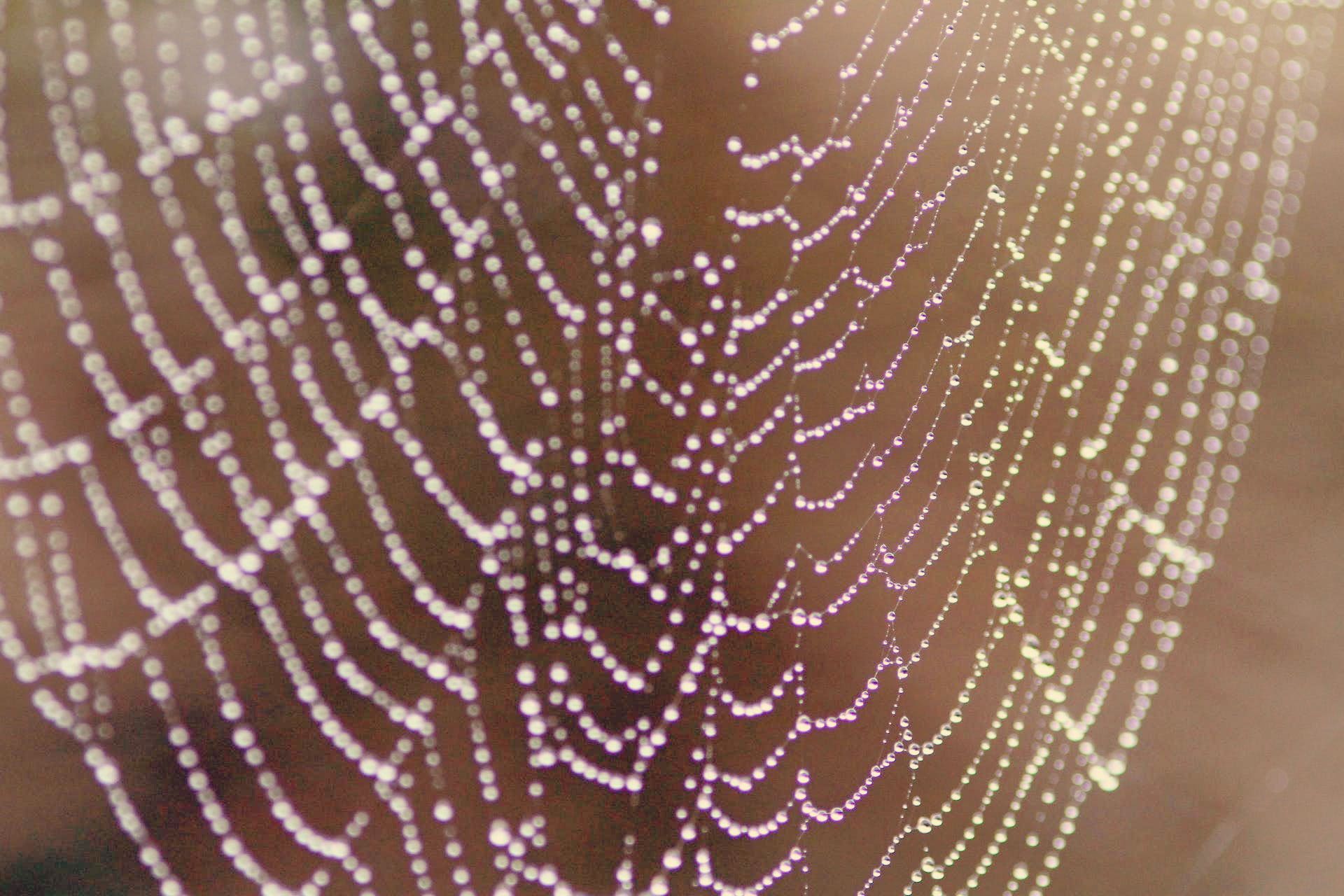
From postdoc to co-founder
The work being carried out by Professor Vollrath and his team at the University of Oxford has provided collaboration opportunities for many postgraduate students. Dr Alex Woods worked with the team as a post doc researcher after studying Human Sciences as an undergraduate and completing a DPhil in Zoology at the University of Oxford.
After gaining his doctorate and then working with Professor Vollrath’s team, Dr Woods decided to train to become a surgeon. While carrying out his training, he combined his medical skills with an in-depth knowledge of silk to launch Newrotex, a spinout from Oxford Biomaterials.
The aim is to launch a medical device in which silk threads help two ends of a severed nerve knit back together. Dr Woods is convinced that silk holds the key because it is strong enough, and yet flexible, to act as a scaffold along which a nerve can grow.
There are several benefits to this approach: the silk is very similar to collagen, which the body uses to repair nerve damage; it is readily accepted by the body so there is less concern around immune response; and it is biodegradable so does not need to be removed.
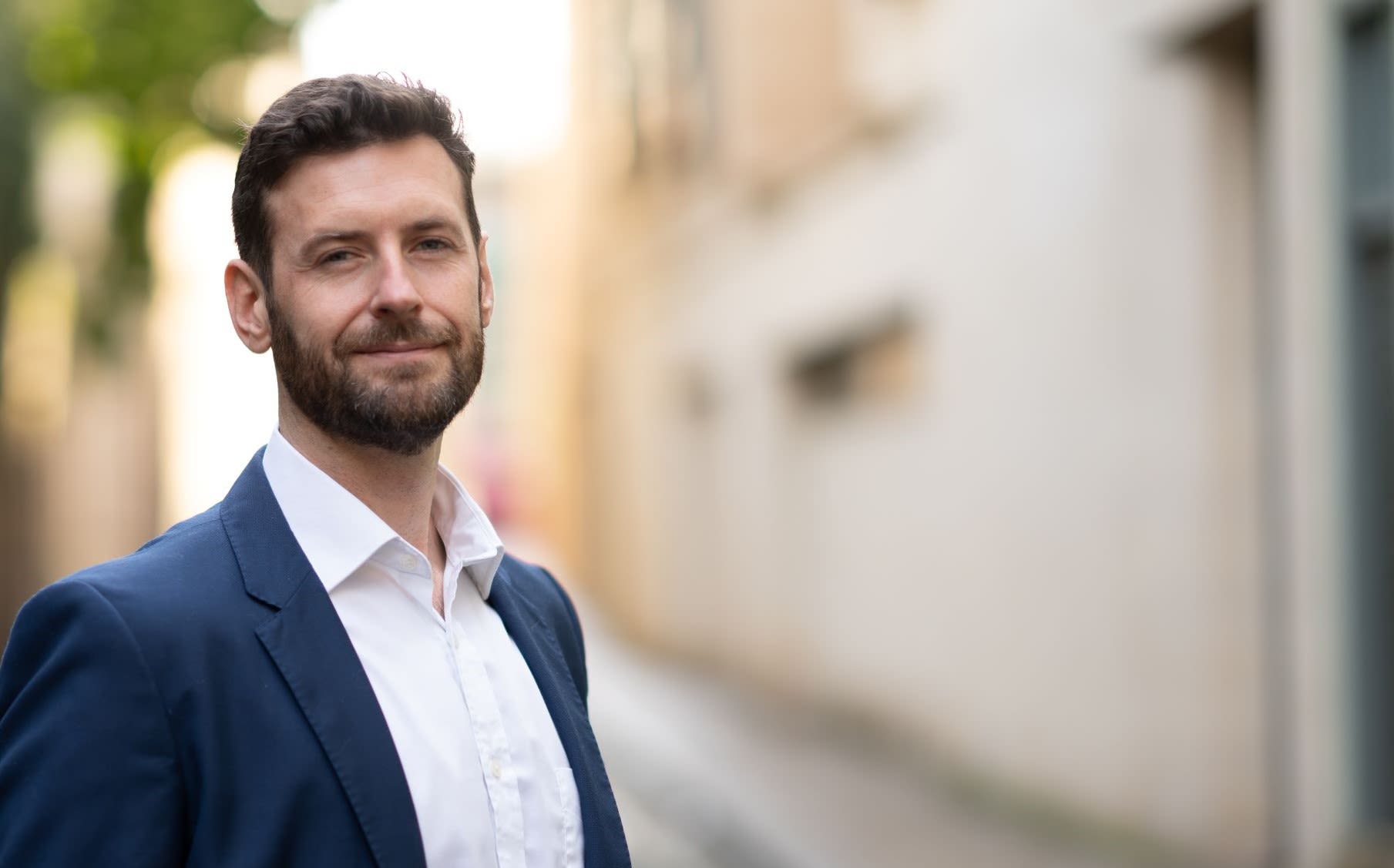
Surgery without the sacrifice
The Oxford team was originally collaborating with Queen Mary University of London but personnel changes meant that the work ended. Dr Woods is now carrying on the project through Newrotex with the help of grant-support from Innovate UK, NiHR and most recently the EIC Accelerator program.
‘Nerves are essentially like a telephone wire, a tube with little wires down the middle that carry information,’ Dr Woods says.
‘They can recover from being knocked and bruised but if they are cut, through a trauma injury or surgery, only around 40% can be repaired by being stitched back together. For the rest, you have to sacrifice a nerve from another part of the body, which can be cut out and grafted to join the two severed nerve ends, but this is not ideal. It involves surgery with a result that is not guaranteed, and means sacrificing a nerve which causes permanent numbness in another part of the body. It can also cause further long-term complications from the donor site, such as chronic pain.'
The further problem with graft surgery is that it requires at least two operations per patient (to remove and then insert a scarified nerve). This requires the availability of specially trained surgeons and increases delays to treatment and medical costs.
The alternatives that have been tried include using nerves from a cadaver, a dead human body, but the material needs to be stored at very low temperatures, has high costs and is not always practical. In some cases hollow tubes have been used that can be inserted in the gap where the nerve has been cut, but they haven’t been successful where there are significant gaps because they don’t provide the internal support to allow nerves to regenerate.
Dr Woods explains that the Newrotex device addresses these challenges as it can be inserted by most surgeons at low cost.
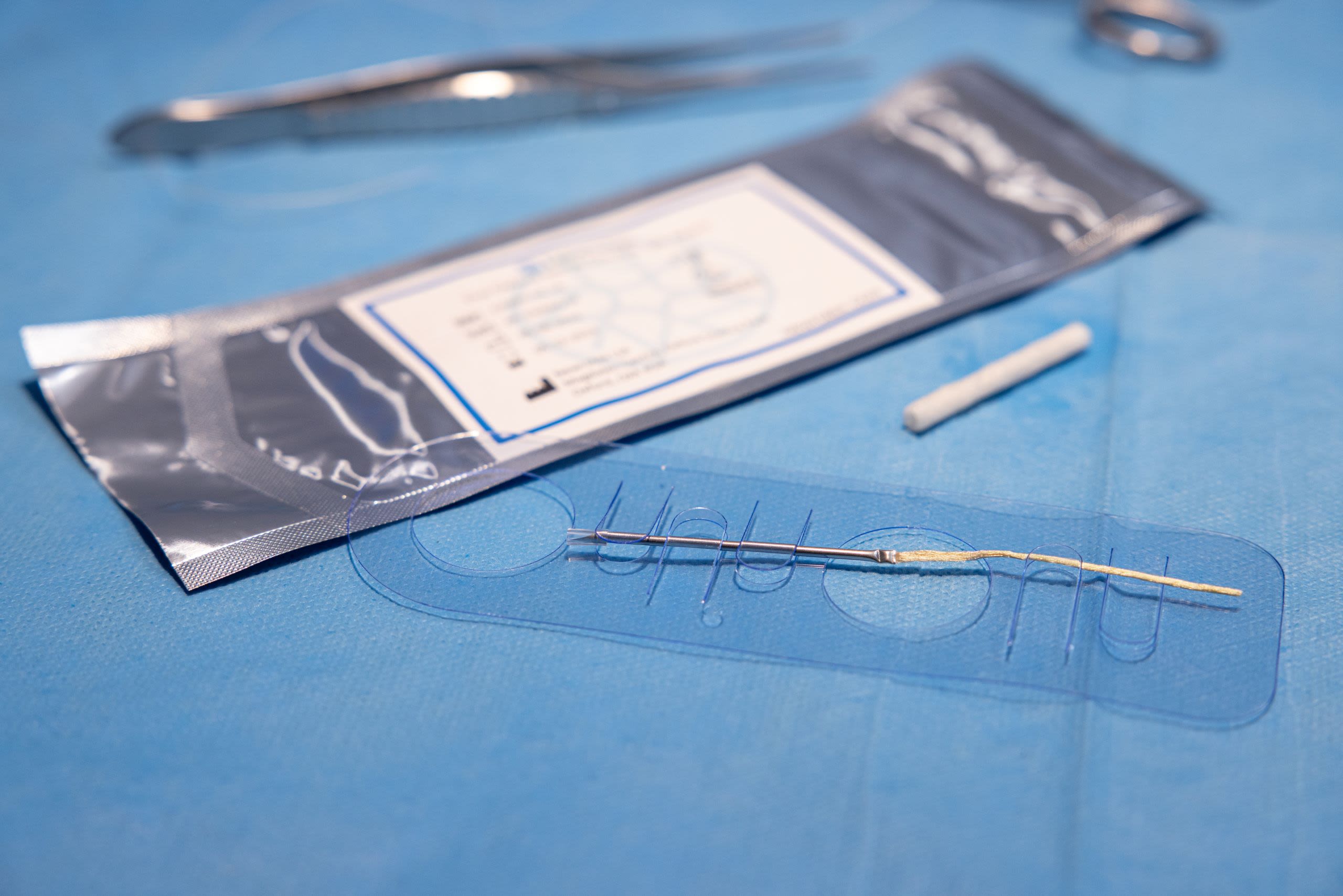
Newrotex silk casing kit
Newrotex silk casing kit
‘The ideal device is something that doesn't require a very high level of skill, and can be used easily by multiple surgical specialities to improve the number of patients and types of injury that can be treated. You want something that even someone like me, as an orthopaedic surgeon used to large tools, can insert easily,’ he says.
‘We've essentially got a silk tube which comes from moths and because there’s an entire agriculture industry around silk, it’s quite easy to get hold of.'
'The silk works well because it’s permeable enough to allow nutrients through to encourage healing but not so permeable that scar tissue can breach it and stop the nerve recovering. It obviously needs to be flexible so it doesn’t get stuck in muscles, and needs to bend without damaging the tube.’
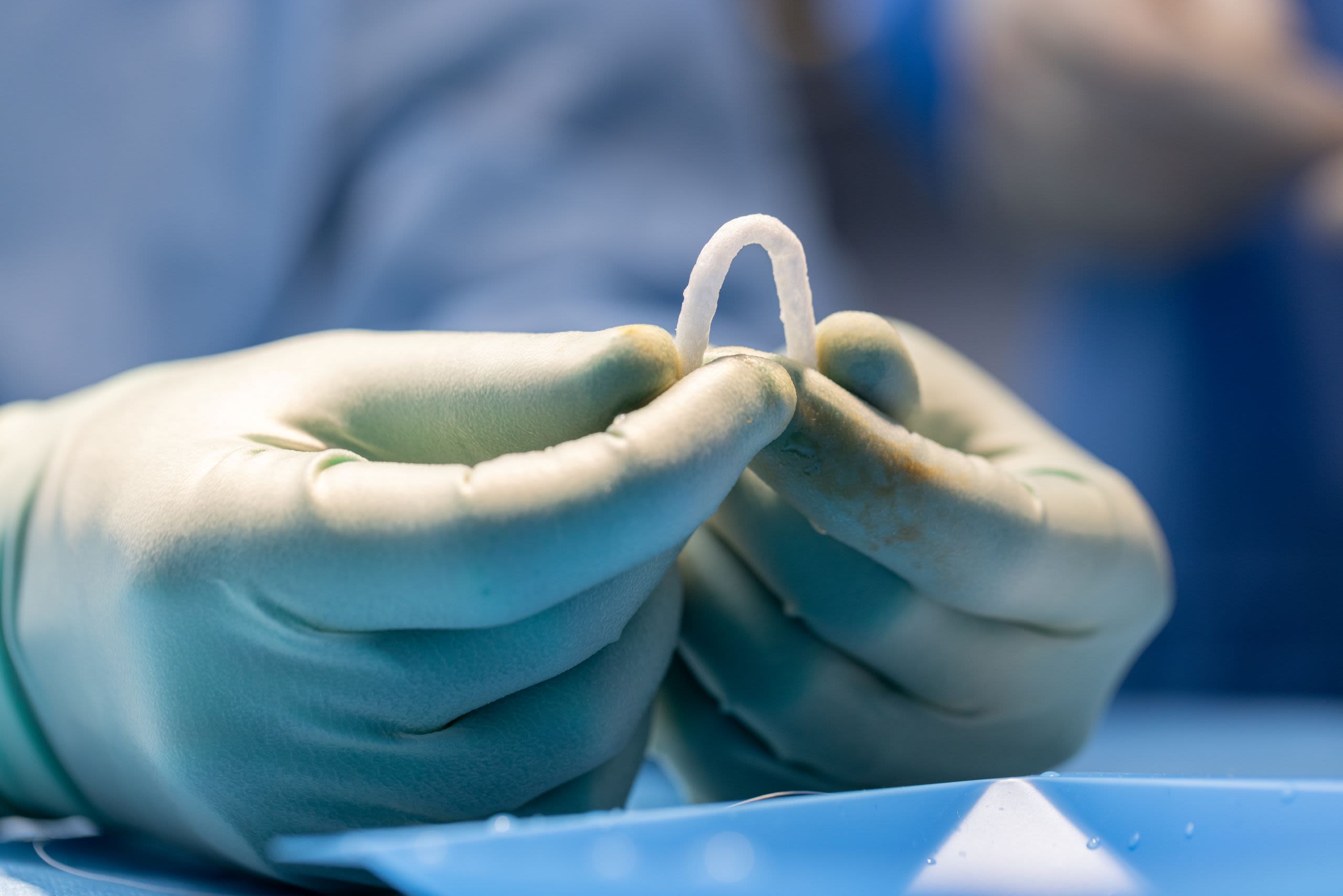
Credit: Newrotex
Credit: Newrotex
While the outer casing being used in experiments is made of silkworm silk, Newrotex is evaluating whether the silk fibres inside the case should come from silkworms or spiders. It is convenient to rely on silkworms because they come from an established industry and, importantly, don’t eat each other. However, spider silk shows some very promising attributes that merit consideration.
One of Professor Vollrath’s breakthroughs at the University’s Department of Zoology (now Biology), as well as the spinouts OBM and Newrotex, was not just to unravel the secret of how spiders spin silk but to discover how they spin seven different types of silk. The fibres used for wrapping up prey, spinning a web, dangling from a ceiling or protecting eggs are emitted from different holes in a spider’s abdomen, and each has its own properties.
The spider silk of most interest to Dr Woods is the ‘drag line’ spiders use to descend. It is strong and flexible and often eaten by a spider once they have finished descending, which indicates why it is able to be easily reabsorbed by the human body. To produce the drag line silk, golden orb spiders are stimulated with a tiny brush at the specific orifice. The silk is then produced and rolled onto a spindle as it is ejected from the spider.
The company reveals that testing has gone well in animals and it is now time to move on to safety and efficacy tests in humans. There are devices already approved by the FDA that wrap around nerves to help them mend and Dr Woods is convinced their performance could be much improved by adding a silk ‘hand rail’. A first step into the market may be to provide silk fibres for placement inside existing devices before a device with both silk casing and silk fibres is approved and made commercially available.
If human trials prove the approach is both safe and beneficial, Dr Woods estimates that the device could be in use to help patients as early as the end of 2025.
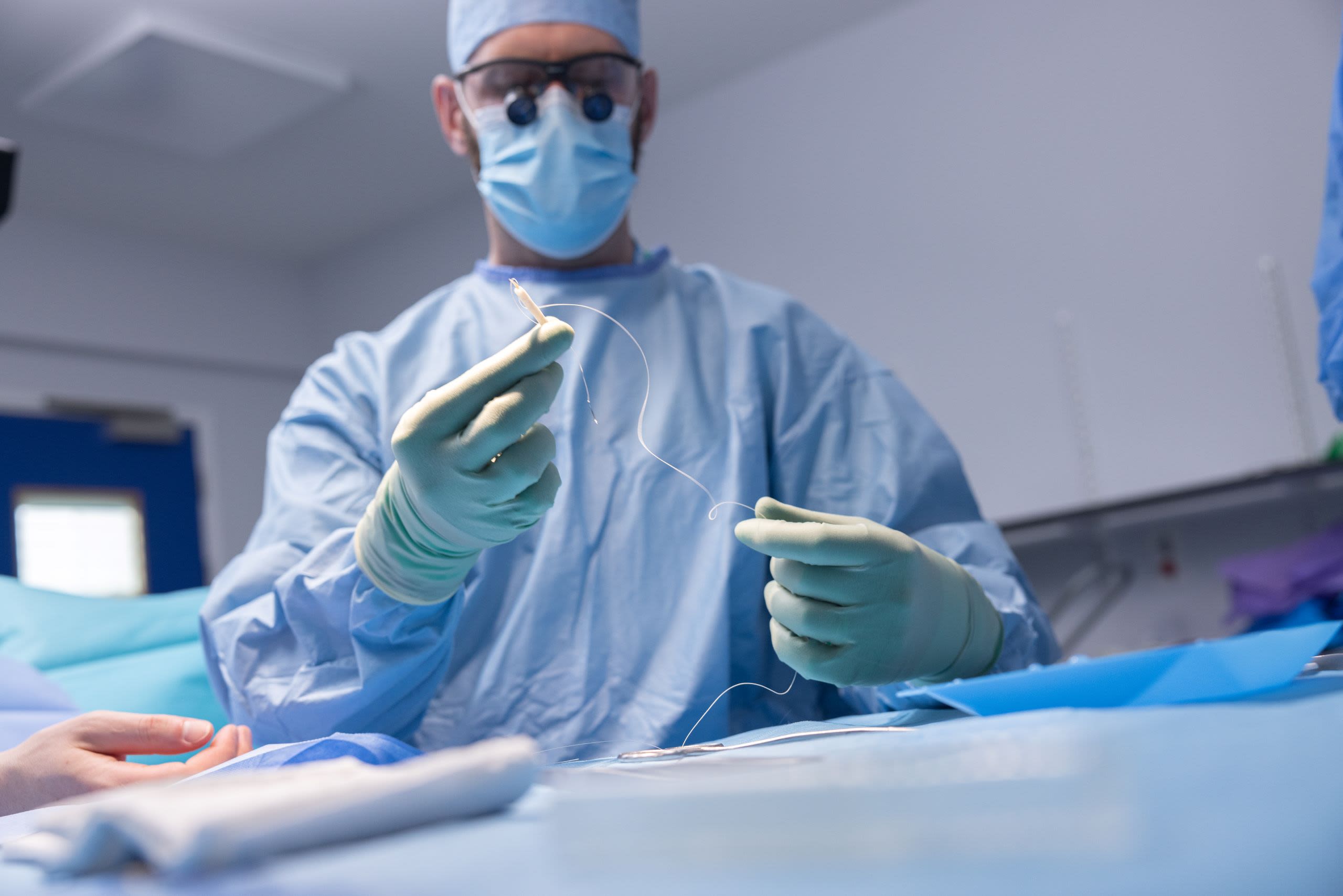
Environmentally friendly fabrics
Another application for Professor Vollrath’s spider discoveries and the ongoing research it has prompted, could be coming soon to the textile industry. University of Oxford spinout, Spintex, has developed a process which mimics the spinning process used by spiders to make webs, to produce a more sustainable, artificially spun silk at a commercial level.
Co-founder, Alex Greenhalgh, believes that mimicking how spiders spin a dragline to descend from a ceiling will prove a far more environmentally friendly way of producing silk. By pulling the replica molecules which Spintex has created into fibres, far less heat, energy, water and chemicals are consumed than those currently used by the silk-production industry.
Greenhalgh worked with Professor Vollrath’s Silk Group ten years ago before moving on to a post in oncology clinical trials at the Churchill Hospital in Oxford. A chance meeting with Professor Vollrath brought Greenhalgh back to the Department of Zoology to carry out further research into how the spinning of spiders could be replicated and applied commercially for environmental impact. Through the pan-European EIC project FLIPT, this research eventually led to the creation of Spintex.
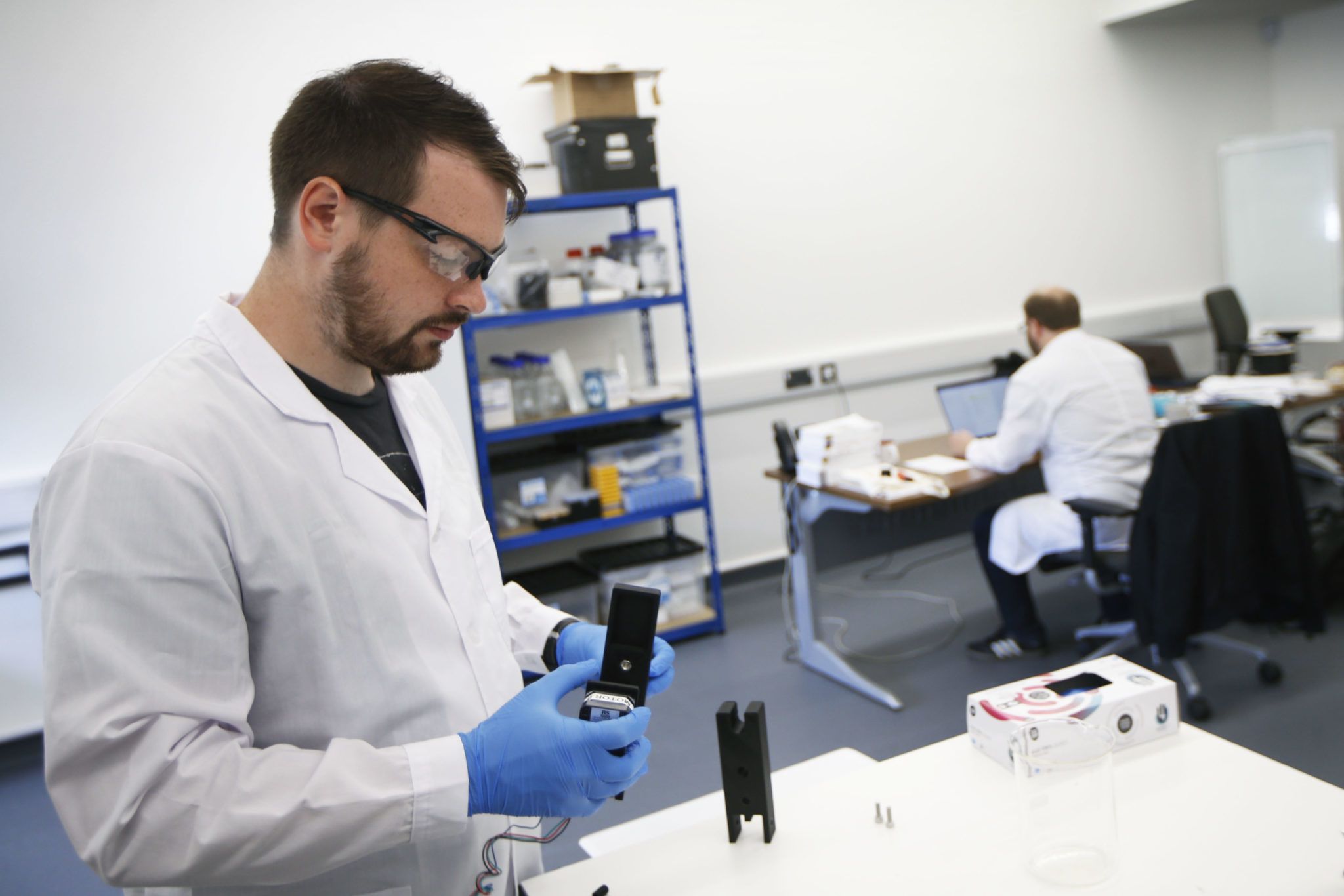
Credit: Spintex Engineering Ltd
Credit: Spintex Engineering Ltd
According to Greenhalgh, there are many advantages to using silk in clothing. Humans have spun it from silkworms for millenia because it is strong, feels luxurious and is naturally cooling due to its ability to ‘breathe’ and wick sweat away from the skin. However, he believes that silk production, like much of the textile industry, needs to become far more environmentally friendly.
‘There are some big advantages, particularly if we compare our process against traditional silk. We consume much less energy in production and reduce the amount of chemicals needed. This means we can tackle some of the main pollution hotspots caused by the textiles industry.
'We have a highly modifiable starting point so there are ways that we could potentially chemically adjust our materials to have unique properties that, at the moment, are only offered by certain plastics or expensive advanced materials. That means we could eventually start replacing some of the plastics we see in clothing as well.’
The team has demonstrated that the process can replicate biological silk spinning. To do so at a commercial scale will take some years, but the next steps of producing samples, in the form of scarves and handkerchiefs, is already underway.
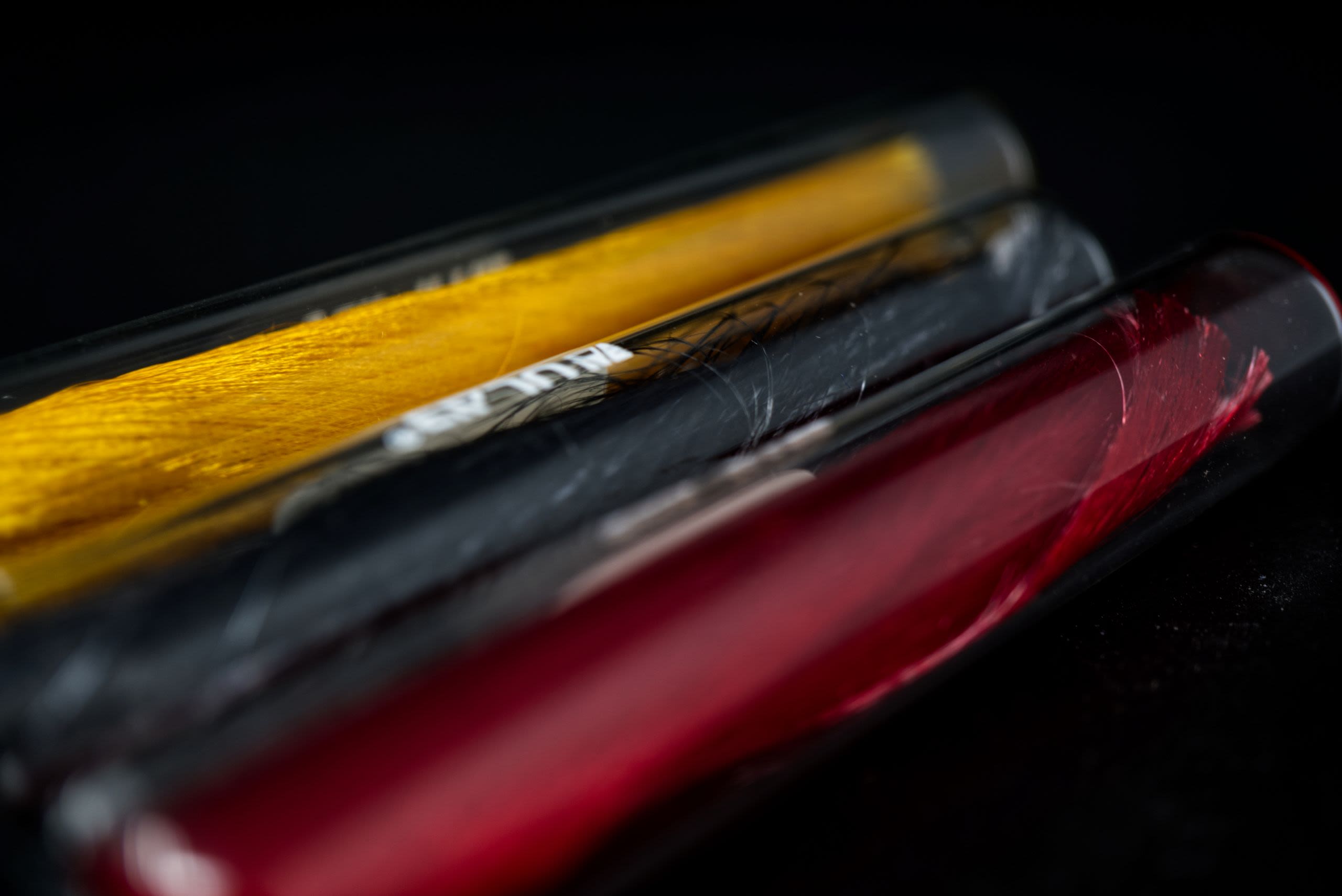
Spintex fibre samples Credit: Spintex Engineering Ltd
Spintex fibre samples Credit: Spintex Engineering Ltd
For Greenhalgh, the encouraging progress the company is making is testament to how the University of Oxford empowers researchers to make a real-world impact.
‘Working at the University of Oxford with Professor Vollrath was amazing because he is one of, if not the world’s most renowned experts in the field of silk,’ he says.
‘I liked the idea of there being applications from research. I could never be just a pure academic who does something purely for the sake of knowing. I want there to be a practical application, and silk is still so full of mystery with so many questions waiting to be answered. It has the potential for many practical applications - from textile production to medical composites to reducing environmental impact - it's got uses in so many areas. It's super fascinating and there's also a real end result that can improve people's lives.’
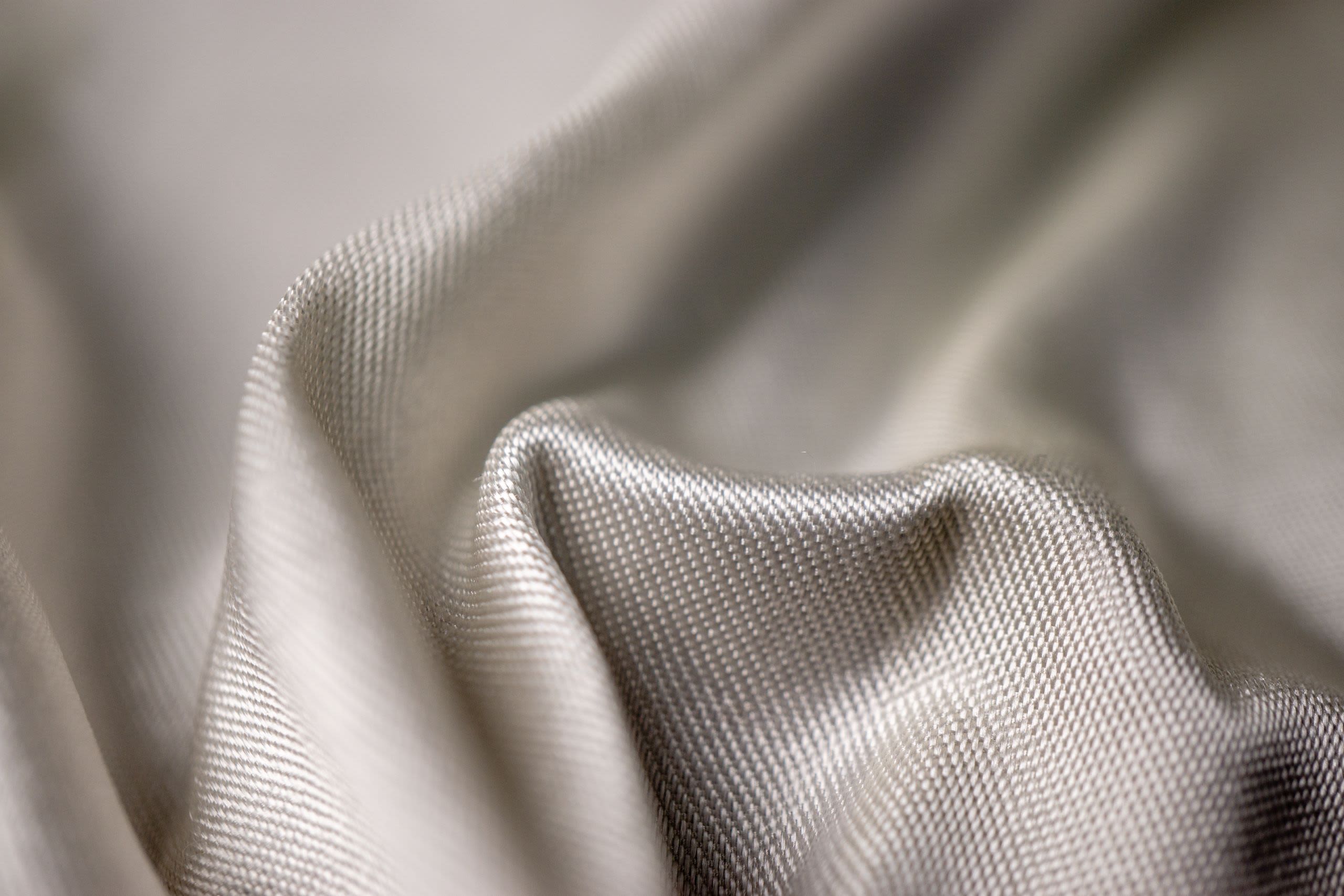
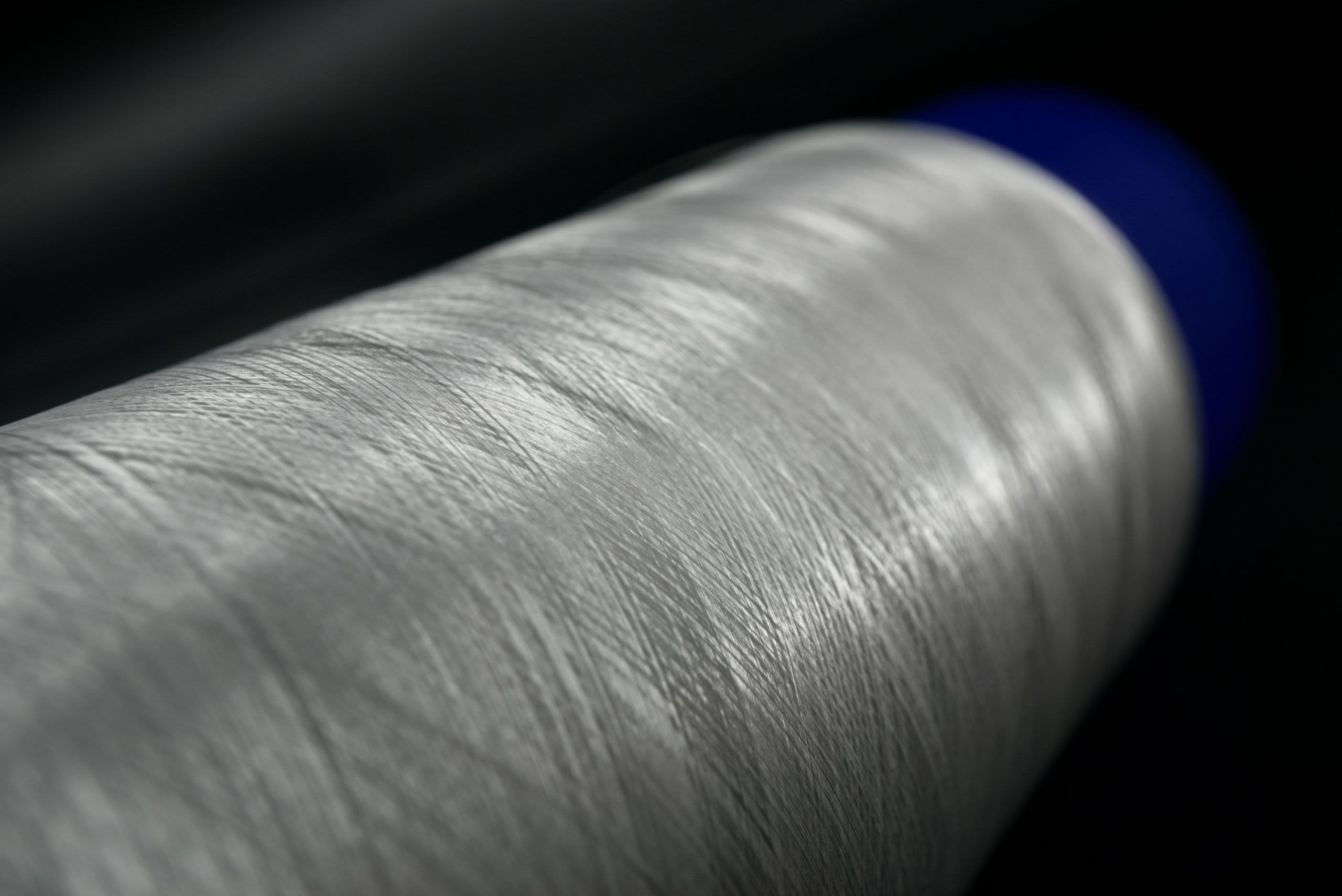
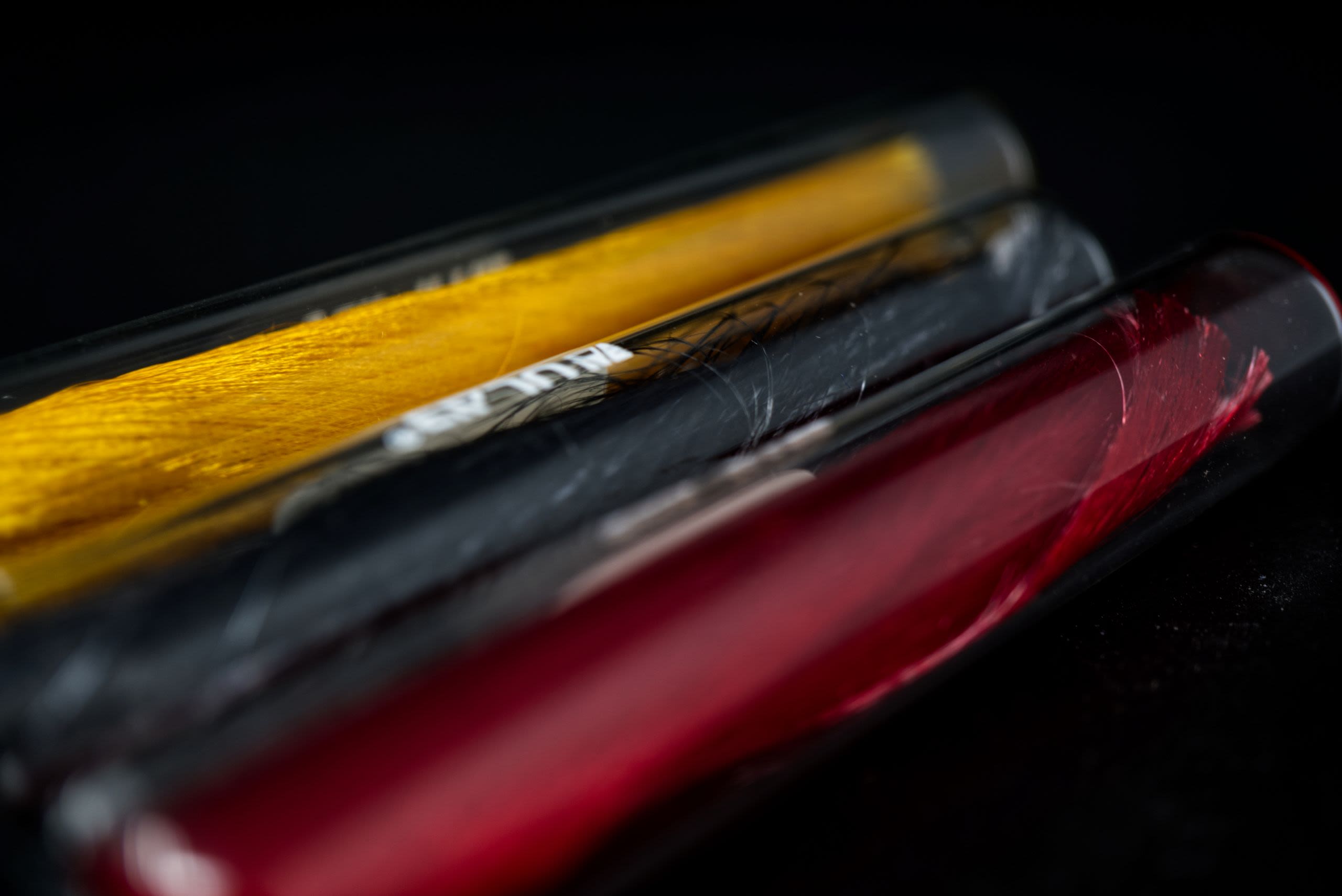